Master Lean Leadership and Operational Transformation
Ideal for Managers and Leaders driving change through lean methods. Suitable for operations, supply chain, finance, and quality roles.
Why Should You Attend?
You’ll Earn New Valuable Skills
- Develop advanced problem-solving skills
- Learn Lean leadership and operational transformation
- Apply Hoshin Planning for strategic direction
- Conduct practical value stream mapping
- Transition from “Doing Lean” to “Being Lean”
You’ll Have Fun Doing It
- Mentorship and Immersion
- A practical learn-as-you-do approach to the Lean
- Black Belt principles and practices
- Experienced practitioners that will give you the most from the course materials
- Access to their extensive real-world knowledge
You’ll Gain Lifelong Knowledge
- Key concepts of Lean thinking and benchmarking
- Application of Hoshin Planning
- Practical value stream mapping exercises for process improvement
- Importance of people development in change management
About this Course
Course Format
Participants have the opportunity to drive large Lean projects. Lean methods taught on the course will be implemented on these projects. Methods include:
- Performance metrics
- Waste reduction
- Quality management
- Root cause analysis
Experience an engaging and dynamic learning process.
Download The Blackbelt Brochure!
Difficulty
%
Intermediate Level
Self Directed
Full Days
On-site
Full Days
Funding
%
Funding Is Available
Course Overview
Session 01 - Lean Thinking & Problem-Solving
This session focuses on the evolution of Lean Thinking. Here you will gain knowledge of Lean Principles using problem-solving. This will build the process skill, supporting the organisation’s purpose.
Key learnings
- The mindset needed to apply Lean Thinking in the Digital environment.
- The application of Lean Thinking to transform your business.
- How the Lean Principles together can help to shape your “Lean Enterprise“.
- Understanding the dimensions of the LBS Partners Transformation Framework.
- The role of structured problem-solving in business transformation.
- Leading a problem-solving culture.
- A deep-dive into
- – problem-solving methodologies,
- – project management
- – A3 thinking.
-
within the context of Operational Excellence.
Session 02 - Strategic Direction & Managing Visually.
This session introduces the tools that define the organisation’s Purpose.
- Hoshin Planning
- Value Stream Mapping
- OKR’s
These tools are critical in the implementation of Lean & Digital Thinking.
Key Learnings
- How to develop a Lean Transformation Pathway & define the Purpose.
- How to use
– Hoshin Planning (Kanri)
– kaizen
– DMAIC
to convert strategy to action through focus & resource planning. - The use of OKRs and how they deliver the Strategic Plan.
- Value Stream Map construction to ensure fulfillment of customer requirements.
- How can Lean & Digital Thinking be used in your company.
Session 03 - Sustaining Lean & Aligning the Team.
This session focuses on building sustainable systems. This is achieved through the application of the dual concepts;
“the Manager as a coach”.
These are key elements of the Transformation Framework, Leadership & Mgmt. System.
Key learnings
- The definition of Enterprise Excellence & its benefits.
- Benchmarking against top companies. Revealing how to foster self-directed learning and create the best strategy.
- How Visual Management of the workplace empowers people. This enables, “Management-by-Sight”.
- How Leader Standard Work promotes standardisation & drives problem-solving
- Monitoring performance against plans. How using Short Interval intervention fuels Continuous Improvement
- How a manager-coach approach can make problem-solving a habit.
Session 04- Digitalisation & Systems for Management.
This session tackles the key challenges of business planning and digital transformation.
Key learnings
- Create proactive Sales & Operations Plans (S&OP), uniting teams.
- How to develop an Integrated Business Planning process.
- To understand the building blocks of a Digital Transformation.
- Understanding the benefits of an ERP system
- A deep dive into the building blocks of a successful ERP deployment.
- Creating a shared vision for success through ISO standards and frameworks.
Session 05 -Change Management & People Management.
Creating the right environment through trust, respect & cognitive safety.Learn how to develop a change-oriented culture in the company. Enhance peoples performance through effective leadership and manage change.
Key learnings
- To understand the nature of change and its challenges.
- How to successfully plan & implement change in a company.
- How to create the right environment, the role of trust, respect & psychological safety.
- The key skills necessary to manage & develop people.
Session 06 - Leading Cultural Change.
How leadership is defined & the role & duties of a leader. Build winning teams with Leadership skills needed to foster a positive culture.
Key learnings
- How leadership is defined & the role & responsibilities of a leader.
- Creating a culture, effective communication & providing support.
- Knowledge of the fundamental attributes of a team.
- Exploring the stages involved in developing a successful team.
- How to develop and retain a high performing team.
Our Results Speak for Themselves
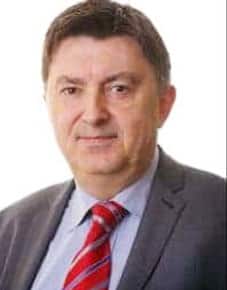
Eddie O’Neill
Training Manager & Lean Consultant
A Training Manager and Lean Consultant at LBS Partners. Specialising in Lean methodology across various industries. Eddies has extensive experience in coaching, training, and mentoring.
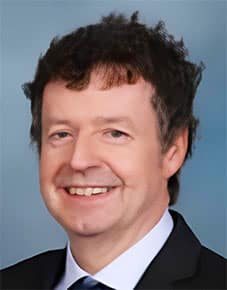
Gerry Shaw
Lead Consultant
A Lead Consultant at LBS Partners, with over 30 years of experience. Specalises in Agile/Lean practices and continuous improvement. He has extensive experience in the software and IT sectors.
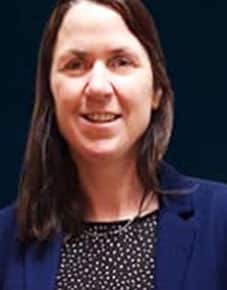
Jane Wickham
Energy & Sustainability Consultant
An Energy & Sustainability Consultant at LBS Partners. Jane has over 15 years of experience. She has experience developing energy management projects. She collaborates with community groups, businesses, and public sector.
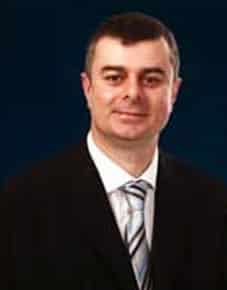
Damien Morris
Lean Digital Consultant
A Lean Digital Consultant at LBS Partners, has over 20 years of experience. Versed in operational excellence, Lean methods, and ERP systems. He has worked with global companies and SMEs to drive sustainable improvement
Frequently Asked Questions (FAQ)
Who is this training for?
Empower leaders with Lean Black Belt training for transformative change. For managers and leaders with engineering backgrounds.
Why should I attend this training?
Lean Black Belt will help you transition to a leader. Become a Problem-Solving Leader of Continuous Improvement.
The participants will:
- develop problem-solving skills
- learn to eliminate waste
- learn how to drive continuous improvement
- gain leadership skills
- achieve measurable business improvements
What Are the Requirements for Lean Black Belt Training?
There are no formal requirements. A Lean Green Belt or equivalent experience is recommended. This is an advanced Lean course.
How Is the Training Delivered?
Our Lean Black Belt Training is delivered across six two-day sessions. Each session consists of two consecutive days of training. The duration of the course is 6 months. Participants are expected to complete 40-70 hours of self-directed hours.
What Is the Duration of the Training?
The course spans 12 days for on-site training and 10 self directed training
What will I learn?
In our Lean Black Belt Training (also known as Black Belt Lean Six Sigma), you’ll learn
- Advanced problem-solving skills
- Lean leadership
- Operational transformation techniques.
The course covers:
- Key concepts of Lean thinking and benchmarking
- Application of Hoshin Planning
- Practical value stream mapping exercises at a healthcare facility
- Importance of people development in Lean transformation
This training ensures you understand how to drive effective change.
What Kind of Certification Will I Receive?
You will receive a Lean Black Belt certification (Black Belt Six Sigma). This demonstrats your ability to lead and sustain Lean transformations.
The course will be accredited by University of Limerick. NQF level 9 with 6 ECTS credits
Are There Any Real-World Examples Included in the Training?
Yes, the training includes practical applications. These will help illustrate the real-world use of Lean principles.
Can This Training Be Customized for My Organization?
We tailor our training programs to the specific goals of your company.
Is There Any Support Available During the Training?
Participants receive guidance from our experienced lean consultants.
How Much Does the Training Cost?
Pricing can vary depending on the specific needs of your company. Please contact us directly for the most up-to-date pricing information.
We are pleased to offer flexible payment options. Financing is available of up to 50% of the training cost. For detailed pricing and funding options, please get in touch with our team.
How Can I Enroll in the Training?
To enroll, please fill out the form on the right and we will follow up shortly.
Let's Get Started!
Get In Touch To Discuss
- Custom Options
- Training Format
- Pricing
- Financing Options
Looking forward to working with you!
Download Our Brochure?
Leave your name and email and we will send an information pack to your inbox.